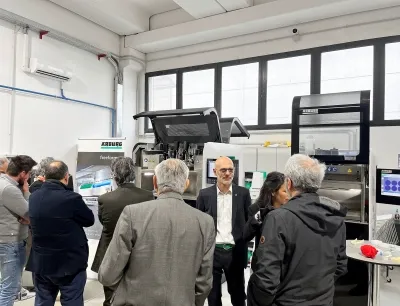
Am 02. März 2023 wurde das Additive Centers „Faberlab powered by Arburg“ im Rahmen eines Open-House-Events feierlich eröffnet. Das Center bei Faberlab, Dienstleister für die industrielle additive Fertigung, bietet Unternehmen über die Region hinaus die einzigartige Gelegenheit, die additiven Maschinen von Arburg und „innovatiQ“ praxisnah kennenzulernen. Kunden profitieren in Orrigio im Großraum Mailand vom gebündelten Wissen und der engen Zusammenarbeit von Faberlab und Arburg. Es geht dabei aber nicht nur um die Technologie an sich, sondern auch um alle möglichen Dienstleistungen rund um die industrielle additive Fertigung und über die gesamte Wertschöpfungskette von der Entwicklung bis zur Fertigung. Dazu gehören etwa das Rapid Prototyping, das Bauteil-Design, aber auch Schulungen.
Dies kann bislang kein anderes italienisches Zentrum Unternehmern, Forschungszentren oder Bildungseinrichtungen anbieten. Dazu stellt Arburg einen Freeformer 200-3X, einen Hochtemperatur-Freeformer 300-3X sowie einen „innovatiQ TiQ 5“-Drucker mit großem Bauraum zur Verarbeitung von Hochleistungs-Thermoplasten zur Verfügung. Von Arburg-Seite aus steht den Additive-Kunden Ivan Panfiglio, Manager für die additive Fertigung in Italien, als Ansprechpartner zur Verfügung.
Dieses Pilotprojekt entspricht dem Arburg Prototyping Center (APC), dass das Unternehmen in der Zentrale Loßburg sowie den Niederlassungen in den USA und China betreibt. Auch in Italien können die Kunden jetzt Benchmark-Bauteile herstellen und Materialien qualifizieren lassen. Damit hat Arburg die Reichweite seiner AM-Aktivitäten strategisch weiter ausgebaut und kann ab sofort auch gezielt auf die lokalen Anforderungen und Bedürfnisse des italienischen Marktes eingehen.
Zentrum für Additive Manufacturing operativ
Zur Eröffnung des „digitalen Labors“ in Orrigio waren insgesamt 118 Gäste zu Beratungen, zum Netzwerken und zu Fachdiskussionen mit den Spezialisten anwesend. Eltek, ein Arburg-Kunde aus Casale Monferrato, stellte den Besuchern eine Fallstudie vor, in der Produkte präsentiert wurden, die auf dem freeformer entstanden sind. Massimo Zanin, leitender Entwicklungsingenieur bei Eltek, hält dazu fest: „Eltek verfügt über rund hundert Arburg-Spritzgießmaschinen. Dadurch sind wir mit Faberlab und dem Freeformer in Kontakt gekommen. Für uns ist das eine ganz besondere Maschine, kein klassischer Filament-3D-Drucker. Für Kunststoffverarbeiter wie uns ist es wichtig, ein System zu haben, das die Prototypen-Herstellung mit den gleichen Kunststoffen wie beim Serienprodukt erlaubt. Unsere Prototypen sollten annähernd die gleichen mechanischen Eigenschaften wie das Original haben.“ Der Freeformer sei der Drucker, der diese Anforderungen am besten erfüllt. Faberlab und Arburg hätten Eltek gemeinsam beim bestmöglichen Einsatz der Maschine geholfen.“
Ein Eltek-Produkt, das vollständig auf dem Freeformer aufgebaut wurde, hat der Forschung einen großen Schub gegeben. Es handelt sich dabei um ein Schnell-Antibiogramm, also ein mikrobiologisches Testverfahren, das die Analyse des Ansprechens eines Bakteriums auf ein Antibiotikum erlaubt. Das ermöglicht, die Pathologie des Patienten sehr schnell zu verstehen und auf diese Weise Leben zu retten.
Stimmen zur Eröffnung
Dr. Victor Roman, Geschäftsführer „ARBURGadditive“ aus Loßburg, kommentiert die gemeinsame Arbeit in Italien so: „Die 3D-Technologie und ihre Verbreitung ist von grundlegender Bedeutung in einer Zeit, in der Unternehmen Innovationen benötigen, um den Zeit- und Kostenaufwand für die Realisierung von Projekten zu reduzieren. In diesem Sinne ist die entstandene Partnerschaft mit Faberlab ein integraler Bestandteil dieses Prozesses und ein Element, das wir für den gesamten italienischen Markt als strategisch betrachten.“
Raffaele Abbruzzetti, Geschäftsführer bei Arburg in Italien, sieht die Kooperation ebenfalls positiv: „Es ist eine wichtige Zusammenarbeit zwischen zwei unabhängigen Unternehmen, aber mit dem gemeinsamen Interesse, die additive Fertigung und ihre Perspektiven mit Maschinen und vor allem dem Start der Produktion auf Abruf anzubieten. Auf diese Weise hat Arburg die Möglichkeit eröffnet, Muster zu fertigen und neue Materialien auf Wunsch italienischer Kunden direkt vor Ort zu qualifizieren. Faberlab kann seine über Jahre gesammelte Erfahrung jetzt mit einem kompletten Maschinenpark nutzen. Deshalb kann ‚Faberlab powered by Arburg‘ in einer so wichtigen industriellen Region wie der Lombardei und auch darüber hinaus eine aktive Rolle bei der Unterstützung von Industrie, Institutionen und Forschungszentren spielen.“
Auch Davide Baldi von Faberlab lobt Kooperation und Technik: „Die Zusammenarbeit zwischen Faberlab und Arburg ist eine Chance für beide Seiten. Arburg hat mit dem Freeformer ein innovatives und einzigartiges Produkt entwickelt, das durch diese Partnerschaft promotet werden kann. Faberlab steuert ein Labor wie kein anderes bei, das die additive Technologie in die Unternehmen bringt und die technologische Entwicklung fördert. Darüber hinaus verfügen wir über einen großen Pool an Unternehmen aus der Kunststoffbranche, von denen viele bereits Arburg-Kunden sind. So können die Bedürfnisse beider Partner sehr gut zusammengebracht werden. Der Freeformer von Arburg arbeitet sehr nah an der Produktion und passt als offenes System perfekt zu den Entwicklungszielen von Faberlab. Die Zusammenarbeit ist auch eine Chance für Unternehmen, einer innovativen neuen Technologie näherzukommen.“
Fast alles ist möglich
Im „Faberlab powered by Arburg“ Additive Center in Orrigio lassen sich nicht nur additive Standardbauteile, sondern etwa auch komplexe Funktionsbauteile als Hart-Weich-Verbindungen oder mit Stützmaterial herstellen. Für die Produktion im industriellen Maßstab steht eine breite Palette von Originalmaterialien, Materialkombinationen und Farben auf höchstem Qualitäts- und Stabilitätsniveau zur Verfügung. Zwei von vielen Beispielen sind etwa der 3D-Druck mit ABS für schlagzähe Bauteile mit hoher Oberflächengüte oder die additive Verarbeitung von Sebs, eines TPE mit hoher Elastizität, Weichheit, guter Einfärb- und Formbarkeit.