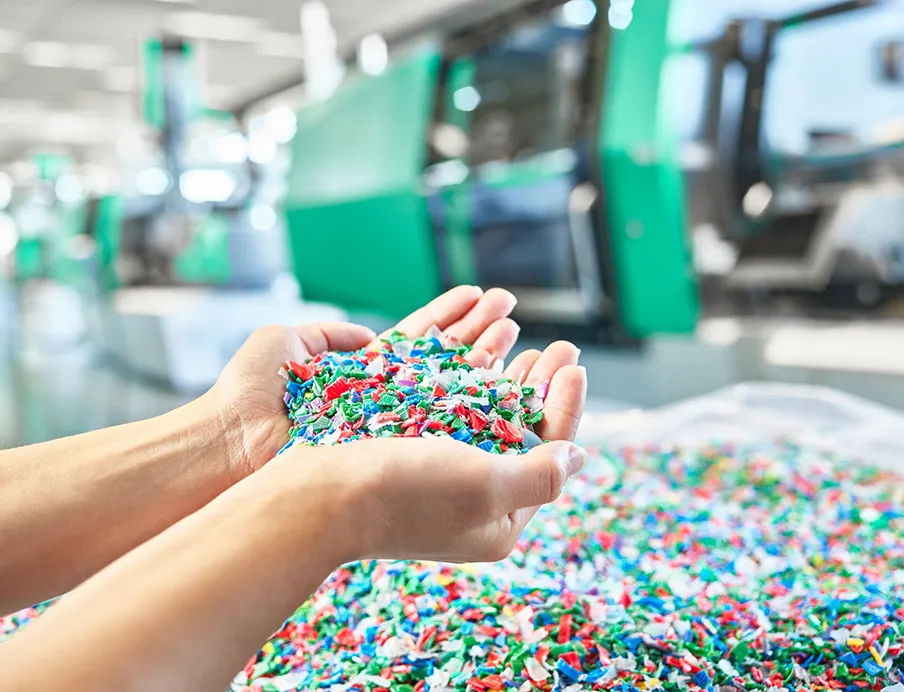
Spritzteile aus Neuware von Schuss zu Schuss und Charge zu Charge reproduzierbar in konstant hoher Teilequalität zu fertigen, ist Stand der Technik. Dies stellt jedoch meist hohe Anforderungen an die Regel- und Steuerungstechnik. Bei der Verarbeitung von Post-Industrial- (PIR) und Post-Consumer-Rezyklaten (PCR) sowie von Biokunststoffen können die Material- und Verarbeitungseigenschaften hingegen stärker schwanken. Für einen effizienten Rezyklat-Einsatz sind daher Regelkonzepte erforderlich, die eine konstante Formfüllung und letztlich eine gleichbleibende Qualität der Endprodukte sicherstellen. Für diese Aufgabe hat Arburg für seine Maschinensteuerungen digitale Pilotfunktionen entwickelt, die in der Einspritz- bzw. Nachdruckphase den Spritzgießprozess stabil halten.
Verschiedene Gremien, Bewegungen und Initiativen forcieren, geschlossene Kreislaufsysteme zu etablieren. Auch wenn sich dies aktuell noch nicht wirtschaftlich rechnet, lautet das Ziel, die Verwendung fossiler Ressourcen mittel- und langfristig deutlich zu reduzieren. In diesem Zusammenhang gewinnt die Verarbeitung von Rezyklaten zunehmend an Bedeutung. Dies ist aber aufgrund wachsender Bandbreite der Materialien, ihrer unterschiedlichen Herkunft und Aufbereitung sowie ihres inhomogenen Verarbeitungsverhaltens anspruchsvoll. Gleiches kann auch für Chargenschwankungen bei Neuware oder für ungenügend vorbereitete Granulate gelten, etwa aufgrund ungleichmäßiger oder ungenügender Materialtrocknung.
Rezyklat vergleichbar effektiv und prozesssicher wie Neuware verarbeiten
Rezyklate sind chemisch betrachtet ebenso Kunststoffe wie klassische Neuware. Der Unterschied ist, dass sie bereits fertige Produkte waren, die eine Nutzungsphase hinter sich hatten und anschließend wieder aufbereitet wurden. Es gibt jedoch noch viele offenen Fragen, ob und wie Rezyklate vergleichbar effektiv und prozesssicher wie Neuware eingesetzt werden können. Die Spritzgießverarbeiter müssen sich hier neuen Herausforderungen stellen.
Herausforderung „Black Boxes“ bei Rezyklat beeinflussen Prozessstabilität und Bauteilqualität
Aus Sicht der Maschine wird beim Spritzgießen mit zwei großen „Black Boxes“ abgearbeitet, welche maßgeblich die Prozessstabilität und die Bauteilqualität beeinflussen. Denn die Maschine selbst weiß weder,
- welches Material in den Trichter eingefüllt wird, noch
- was zwischen den beiden Aufspannplatten passiert.
Dies sind zwei große Herausforderungen, um Prozessparameter wie Temperaturverlauf der Formmasse sowie Temperatur- und Druckverlauf im Werkzeug zuverlässig zu regeln. Der größte Unterschied zur Verarbeitung von Rezyklaten gegenüber Neuware besteht darin, dass die Materialeigenschaften und Kennwerte wie mechanische Qualität, Farbe oder Geruch innerhalb einer Lieferung oder eines Auftrags in größeren Spannbreiten variieren können. Dem recycelten Granulat kann bei den meisten Kreislaufprozessen aktuell keine eindeutige Materialspezifikation zugeordnet werden. Deshalb steht kein Datenblatt beim Einrichten der Maschine zur Verfügung. Das erschwert die Verarbeitung erheblich.
Jedoch gibt es z. B. Pilotfunktionen in der Gestica- und Selogica-Steuerung von Allrounder-Spritzgießmaschinen, die schwankenden Viskositäten in der Schmelze entgegenwirken: Der „aXw Control „ReferencePilot“ und der „aXw Control RecyclatePilot“ können Unregelmäßigkeiten erfassen, zuverlässig ausgleichen und den laufenden Einspritzprozess aktiv regeln. So wird die Formfüllung möglichst konstant gehalten und trotz größerer Variationen für eine gleichbleibende Bauteilqualität gesorgt.
Einflussgröße Aufschmelzprozess zur Herstellung von Gutteilen
Ein homogener und stabiler Aufschmelzprozess ist eine wichtige Einflussgröße, um Gutteile produzieren zu können. Das beginnt damit, dass das Material möglichst gleichmäßig in die Schnecke eingezogen wird. Dabei spielen die Form und Qualität des Rezyklats eine wichtige Rolle. Liegt Granulat vor, lässt sich recycelter Kunststoff grundsätzlich so gut wie Neuware verarbeiten, ohne dass zusätzliche Hardware erforderlich ist. Anders sieht dies bei Flakes und Mahlgut aus. Flakes können in Größe und Form sehr uneinheitlich sein. Mahlgut als Material aus Kunststoffteilen, die nur mit einer Angussmühle zerkleinert wurden, besteht aus verschieden großen Bruchstücken, idealerweise in Korngrößen von zwei bis fünf Millimetern. Begleitet werden diese Körner in der Regel von feinerem bis hin zu staubförmigem Material. Um einen stabilen Aufschmelzprozess zu erhalten, muss Mahlgut entstaubt werden.
Rezyklat-Paket für Verarbeitung von Mahlgut und Flakes
Für die Verarbeitung solcher Materialien gibt es ein nachrüstbares Rezyklat-Paket von Arburg, das Soft- und Hardware-Features zusammenfasst. Zur Software zählen unter anderem mehrstufige Anfahrparameter und die digitale Assistenzfunktion „aXw Control ScrewPilot“. Sie sorgt für eine präzise und stabile Formfüllung. Bei der Hardware-Ausstattung ermöglicht ein modifiziertes Zylindermodul eine unterbrechungsfreie Zufuhr auch schlecht rieselnder Materialen. Eine Plastifizierschnecke mit modifizierter, tiefer geschnittener HC-Geometrie (High Compression) dient einer homogenen Aufbereitung. Dabei fungieren Nuten im Einzugsbereich als Einzugshilfe, damit das Material trotz unregelmäßiger Form stabil nach vorne gefördert wird. Zudem ist die Schnecke CrN-beschichtet, was Belagbildung und Verschleiß aufgrund unerwarteter Fremdkörper reduziert.
Regelkonzept für den Kernprozess „Form füllen“
Ein von Zyklus zu Zyklus reproduzierbares Füllen der Werkzeug-Kavität bildet die Grundlage für eine gleichmäßige Bauteilqualität. Ein erfolgreiches Steuerungskonzept hierfür ist die Pilotfunktion „aXw Control ScrewPilot" bzw. „lagegeregelte Schnecke“. Bei diesem wird der Füllvorgang durch eine geschwindigkeitsgeregelte Schneckenbewegung mehrstufig an die Anforderungen des Fließwegs angepasst. Dieses Konzept lässt sich vergleichen mit dem Fahrassistenten für Pkws. Weicht die Bewegung in der Schnecke durch Störeinflüsse wie Schwankungen der Viskosität in der Kunststoffschmelze von der programmierten Geschwindigkeit ab, wird diese so geregelt, dass trotzdem der Weg in vorgesehener Zeit erreicht wird. Das aktive Beschleunigen und Bremsen gleicht also Störeinflüsse dynamisch aus, sodass eine konstante Schmelzemenge in die Kavität gefördert wird. Vor allem bei hohen Einspritzvolumenströmen bewährt sich diese Dynamik. So lassen sich vor allem durch gezieltes und schnelles Bremsen Druckspitzen und damit Überfüllungen verhindern.
Regelung in der Nachdruckphase
Die Nachdruckphase ist ebenfalls entscheidend für die Bauteilqualität. Sie wird in der Regel als quasi statischer, druckgeregelter Prozess ausgeführt, zu dem zuvor ein Maschinen-Einsteller die optimalen Parameter ermittelt hat. Sowohl kurzfristige Einflüsse in der laufenden Produktion, wie z. B. Viskositätsschwankungen in der Schmelze (hervorgerufen durch Rezyklate, Gleitmittel oder Farbzusätze), sowie langfristig auftretender Verschleiß an der Rückstromsperre und anderen mechanischen Komponenten bleiben dabei unberücksichtigt. Das kann langfristig zu Schwankungen im Werkzeuginnendruck und damit zu unregelmäßiger Teilequalität führen.
Arburg entwickelte deshalb eine in die Steuerung „integrierte Spritzprozessregelung“, welche die Nachdruckkurve über einen Drucksensor im Werkzeug in Echtzeit regelt. Diese Software-Funktion wurde stetig weiterentwickelt zum heutigen „aXw Control ReferencePilot“. Als Basis für die aktive Regelung in der Nachdruckphase, bei welcher der aktuelle Nachdruck dem Innendruck nachgeführt wird, zieht der Referencepilot die Sollwert-Referenzkurve eines Gutteils heran. Als zugehörige Hardware ist ein möglichst angussnah im Werkzeug platzierter Drucksensor erforderlich. Die Funktionsweise ist vergleichbar mit dem Autonomen Fahren: Trotz GPS und bekannter Strecke benötigt ein Fahrzeug zusätzlich aktive Sensoren, um sich sicher im Straßenverkehr bewegen zu können. Denn nur damit lassen sich. unvorhergesehene Unebenheiten, Baustellen oder andere Verkehrsteilnehmer erkennen.
Einflussfaktor Werkzeug-Innendruck
Um Störeinflüssen schnell entgegenwirken zu können und Druckschwankungen aktiv auszugleichen, erhält die Software vom Sensor in Echtzeit erfasste Signale des Werkzeuginnendrucks. Dadurch ist der Referencepilot in der Lage, die Innendruckkurve vom aktuellen Ist- auf den gewünschten Sollwert zu regeln. Bei der Regelung mit dem Referencepilot werden die Druckverhältnisse im Werkzeug von Schuss zu Schuss exakt der Referenz angepasst und dabei der Ist- auf den Soll-Wert gehoben. Resultat sind ein konstantes Schussgewicht und gleichbleibend hohe Teilequalität, ohne dazu manuell in die Prozessparametrierung eingreifen zu müssen.
Kalibrierter Drucksensor erforderlich
Um den Referencepilot nutzen zu können, bedarf es zweier Voraussetzungen:
- Die Spritzgießmaschine muss mit dem „aXw ScrewPilot“ ausgestattet sein, der für elektrische und hybride Allrounder Standard ist.
- In der Werkzeug-Kavität muss genug Platz sein, um einen Drucksensor zu installieren.
Der Sensor verursacht per se einen Mehraufwand; zudem sind Know-how und Zeitaufwand erforderlich, um ihn bei jedem Rüstvorgang neu zu kalibrieren und regelmäßig zu warten. Nur so ist sichergestellt, dass das „Messmittel“ Innendrucksensor voll funktionsfähig ist und die richtigen Signale liefert. Sind alle Anforderungen erfüllt, lässt sich der Spritzgießprozess durch Zusammenspiel von Sensor und Pilotfunktion schnell und zuverlässig stabilisieren. Die Anzahl der Anfahrzyklen kann stark reduziert werden und es fällt weniger Ausschuss an. Resultat sind längere störungsfreie Produktionszeiten, weniger nachgeschaltete Prüfprozesse und eine gesteigerte Produktionseffizienz. Je nach Anwendungsfall kann sich die Investition in Sensorik also schnell amortisieren.
Regelung in der Einspritzphase
Eine Alternative, ist der neue „aXw Control RecyclatePilot“, der den Spritzgießprozess direkt in der Einspritz- bzw. Formfüllphase allein auf Basis von Daten aus der serienmäßigen Maschinen-Sensorik regelt. Im Vergleich zum Referencepilot, der Signale direkt von der Kavität empfängt, ist die Regelstrecke beim Recyclatepilot länger. Dennoch bietet er zahlreiche klare Vorteile:
- Auf zusätzliche Sensoren kann komplett verzichtet werden.
- Die in die Steuerung integrierte Pilotfunktion lässt sich einfach per Knopfdruck aktivieren.
- Die Funktion bedient sich der maschineninternen Sensorik, deren Kalibrierung nur alle paar Jahre fällig ist.
- Diese Pilotfunktion gleicht kurzfristige Schwankungen von Schuss zu Schuss aus sowie zyklusübergreifend.
Prozessregelung per Knopfdruck
Der Bediener optimiert die Prozesseinstellungen zunächst wie gehabt, sodass die erforderliche Qualität des Gutteils erreicht ist. Diese Referenz wird per Steuerungsbefehl an die Pilotfunktion übergeben. Ein weiterer Befehl aktiviert den Recyclatepilot. Dieser analysiert daraufhin das Einspritzverhalten, erkennt markante Punkte und Abweichungen im Spritzprozess und sorgt dafür, dass das eingespritzte Volumen und somit die Formfüllung konstant bleibt. Dazu wird in der Einspritzphase das Ereignismuster im selben Zyklus mit der eingegebenen Referenz verglichen und der Umschaltpunkt gegebenenfalls kurzfristig angepasst. Zudem ergibt sich durch die Korrektur des Dosiervolumens auch langfristig und zyklusübergreifend eine höhere Stabilität des Gesamtprozesses.
Fallbeispiel Haarkamm aus Rezyklat in verschiedenen Materialvarianten
Schwankende Materialeigenschaften und -viskositäten im Spritzgießprozess werden besonders gut ersichtlich, wenn angussfrei und ohne Nachdruck gefertigt wird. Resultat sind unterschiedlich unvollständige Formfüllungen, wie das Beispiel „Haarkamm“ zeigt. Das Bauteil wurde aus PA6 in drei Materialvarianten spritzgegossen, Neuware, Rezyklat in Form von Granulat und als Mahlgut. Das Ausmaß der Formfüllung lässt sich anhand des Teilegewichts nachvollziehen:
- Der Kamm aus Neuware war, da bewusst ohne Nachdruck produziert, im Werkzeug nicht voll ausgeformt und diente als Referenz.
- Beim Spritzteil aus Rezyklat-Granulat blieb das Gewicht konstant, lag aber deutlich unter dem aus Neuware.
- Bei Mahlgut waren zusätzlich starke Schwankungen des Teilegewichts zu beobachten.
Dies änderte sich quasi auf Knopfdruck durch aktive Regelung mit dem Recyclatepilot. Nun war Teilegewicht für alle drei Varianten konstant und nahezu gleich hoch. Mit diesem Fallbeispiel hat Arburg gezeigt, dass die digitale Pilotfunktion die resultierenden Schwankungen in der Formfüllung ausgleicht und dadurch sowohl die Prozesssicherheit als auch die Teilequalität deutlich steigern kann. Aus der deutlich verbesserten Formfüllung ergibt sich weiterhin eine hohe Werkzeugsicherheit.
Fazit: Rezyklat durch intelligente Pilotfunktionen verarbeitbar
Die Steuerung ist der „intelligente“ Kopf einer Spritzgießmaschine und kann den Bediener umfassend und aktiv unterstützen. Mit Hilfe digitaler Pilotfunktionen wie dem Recyclatepilot und dem Referencepilot lässt sich bei der Verarbeitung von Rezyklaten die Prozesssicherheit durch aktive Regelung in der Einspritz- und Nachdruckphase deutlich steigern. Das Einspritzprofil und der Füllvorgang des Formteils bleiben dabei stabil und entsprechen der vorgegebenen Referenz.
Unzureichende Materialeigenschaften von Rezyklaten lassen sich aber natürlich nicht generell überwinden, sodass der Steigerung der Teilequalität Grenzen gesetzt sind. Die Kenntnis und Erfahrung des Anwenders sind noch immmer wegweisend und entscheidend dafür, welches Konzept bei welchem Prozess gute Ergebnisse liefert. In der Zukunft könnten hierbei übergeordnete, KI-gestützte Methoden zusätzlich unterstützen.
Autor
Dr. Thomas Walther
Abteilungsleiter Verfahrens- und Prozessentwicklung bei Arburg